The Bottom Line: Most Common Reasons Construction Costs Get Expensive
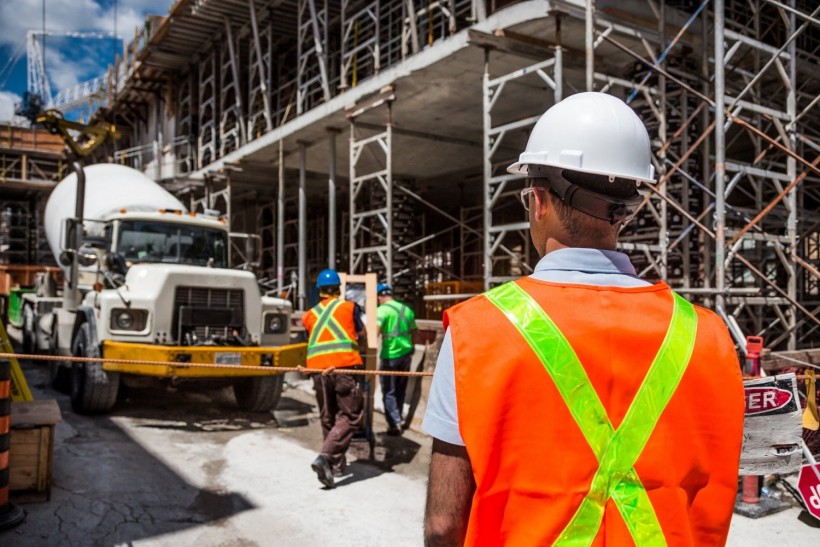
Running a successful construction business is an expensive endeavor. As a business owner or construction site manager, you have to consider the cost of labor, materials, and equipment for every project. In order to make a decent profit, you have to make sure you do not go over the set budget. Unfortunately, there are many conditions that could jeopardize your bottom line. However, understanding what can go wrong is the first step to reducing construction costs.
Most Projects Go Over Budget
If the price of your projects consistently runs higher than you anticipated, you are not alone. According to recent studies, over 85 percent of construction projects exceed their budget to some level. Of course, sometimes issues are out of your control, but there are plenty of things your business can avoid to improve its profitability.
So whether you are running an established construction company or just starting out as a business owner, here are the most common construction mistakes that affect your bottom line.
Poor Site Management
It may seem obvious, but poor site management is one of the leading causes of an inefficient work site. Poor management will result in wasted time, project delays, and a poor quality of work. If your manager is disorganized and fails to keep workers busy, a project will take longer than it should and hurt your bottom line. It is essential to hire a trusted site manager who will stay on top of tasks and keep the worksite running smoothly and efficiently.
Not Shopping Around For Materials
One of the biggest mistakes contractors make is not shopping around for the best deals. Of course, you do not want to sacrifice quality, but finding the best prices is essential to staying within a budget. Instead of going to retail hardware stores, consider purchasing from wholesale dealers or shopping online for tools to compare prices.
Working With Faulty Equipment
Nothing slows a work site down more than working with old unreliable equipment. You may think you are saving money by working with what you have, but constantly repairing old machines can waste time and money. Next time a machine breaks down, consider renting new equipment at a low cost in order so you can get back to work without skipping a beat.
Not Hiring The Right Workers
Hiring the wrong team of workers can affect performance, deadlines, and your bottom line. Workers with poor workmanship or absentee problems can cause major issues on the job site. Paying more in labor costs for reliable help will not only improve the quality of your work but will save you time and aggravation from fixing the mistakes of lousy employees.
Hiring the Right Help
When considering workers for a project, it is essential to check for licensing and proven ability in their field. For example, if you hire a plumber, they should have the right certification and enough experience for the job. A great way to avoid inadequate help is to hire workers and subcontractors you have worked with in the past.
Human Error
There are many ways human error can cost you a lot of money. Workers can accidentally damage a machine which could require a costly repair, or do the wrong task, which would have to be redone. Of course, everyone makes mistakes from time to time, but there are necessary steps you should follow to limit mistakes as much as possible. For example, make sure only qualified workers that understand safety protocols use your heavy machines. You should also always check in on your team to ensure everything is done correctly.
Environmental Delays
One of the biggest issues on any job site is weather days. Of course, you can't control the weather, but keeping an eye on weather patterns can help you decide when to start a project.
Avoid These Common Mistakes
While you can't control everything, having a strong understanding of what can go wrong can help your prepare for any issues you may face on the job site. Study these common mistakes to improve the bottom line of your future projects.
Subscribe to Latin Post!
Sign up for our free newsletter for the Latest coverage!